Comprehensive Guide: What is Porosity in Welding and How to Prevent It
Wiki Article
Understanding Porosity in Welding: Discovering Reasons, Impacts, and Prevention Methods
Porosity in welding is a relentless obstacle that can substantially influence the top quality and honesty of welds. As experts in the welding market are aware, recognizing the causes, effects, and prevention techniques associated with porosity is vital for achieving durable and dependable welds. By delving into the source of porosity, examining its detrimental impacts on weld quality, and exploring efficient prevention techniques, welders can boost their expertise and abilities to produce top notch welds regularly. The complex interaction of factors adding to porosity needs an extensive understanding and an aggressive strategy to ensure successful welding results.Usual Sources Of Porosity
Porosity in welding is primarily triggered by a combination of variables such as contamination, incorrect shielding, and insufficient gas insurance coverage during the welding procedure. Contamination, in the kind of dirt, grease, or corrosion on the welding surface area, develops gas pockets when heated, bring about porosity in the weld. Improper shielding takes place when the shielding gas, typically used in processes like MIG and TIG welding, is not able to completely safeguard the liquified weld swimming pool from reacting with the surrounding air, causing gas entrapment and succeeding porosity. In addition, poor gas protection, usually because of inaccurate flow rates or nozzle positioning, can leave parts of the weld vulnerable, enabling porosity to develop. These factors collectively add to the formation of gaps within the weld, compromising its stability and possibly creating architectural concerns. Comprehending and resolving these typical causes are crucial actions in preventing porosity and guaranteeing the quality and strength of bonded joints.Effects on Weld Top Quality
The existence of porosity in a weld can significantly compromise the total top quality and honesty of the welded joint. Porosity within a weld creates voids or cavities that compromise the structure, making it extra at risk to breaking, deterioration, and mechanical failing.In addition, porosity can hinder the performance of non-destructive screening (NDT) strategies, making it challenging to discover other flaws or stoppages within the weld. This can result in considerable safety and security issues, specifically in important applications where the architectural integrity of the welded elements is critical.

Prevention Techniques Review
Offered the damaging effect of porosity on weld high quality, efficient avoidance the original source strategies are critical to my latest blog post maintaining the architectural honesty of welded joints. Additionally, picking the proper welding criteria, such as voltage, existing, and take a trip rate, can assist lessen the threat of porosity formation. By integrating these prevention methods right into welding techniques, the event of porosity can be dramatically lowered, leading to more powerful and a lot more reliable welded joints.Significance of Correct Protecting
Appropriate securing in welding plays an important duty in stopping atmospheric contamination and making sure the integrity of welded joints. Securing gases, such as argon, helium, or a blend of both, are typically made use of to shield the weld swimming pool from reacting with elements airborne like oxygen and nitrogen. When these responsive components enter call with the warm weld swimming pool, they can create porosity, resulting in weak welds with lowered mechanical residential properties.
Inadequate protecting can result in various issues like porosity, spatter, and oxidation, jeopardizing the architectural integrity of the bonded joint. As a result, adhering to appropriate securing techniques is necessary to generate premium welds with marginal flaws and ensure the long life and reliability of the bonded elements (What is Porosity).
Surveillance and Control Techniques
Just how can welders successfully keep track of and regulate the welding procedure to ensure optimum outcomes and protect against problems like porosity? By constantly keeping an eye on these variables, welders can determine inconsistencies from the suitable problems original site and make instant adjustments to prevent porosity formation.
Additionally, implementing appropriate training programs for welders is essential for keeping an eye on and controlling the welding procedure effectively. What is Porosity. Enlightening welders on the relevance of keeping consistent parameters, such as correct gas securing and travel rate, can help prevent porosity problems. Routine assessments and certifications can also make sure that welders are skillful in surveillance and managing welding procedures
In addition, the use of automated welding systems can improve monitoring and control abilities. These systems can precisely regulate welding criteria, lowering the likelihood of human mistake and guaranteeing constant weld high quality. By incorporating advanced tracking innovations, training programs, and automated systems, welders can properly keep track of and manage the welding procedure to minimize porosity issues and accomplish premium welds.
Final Thought
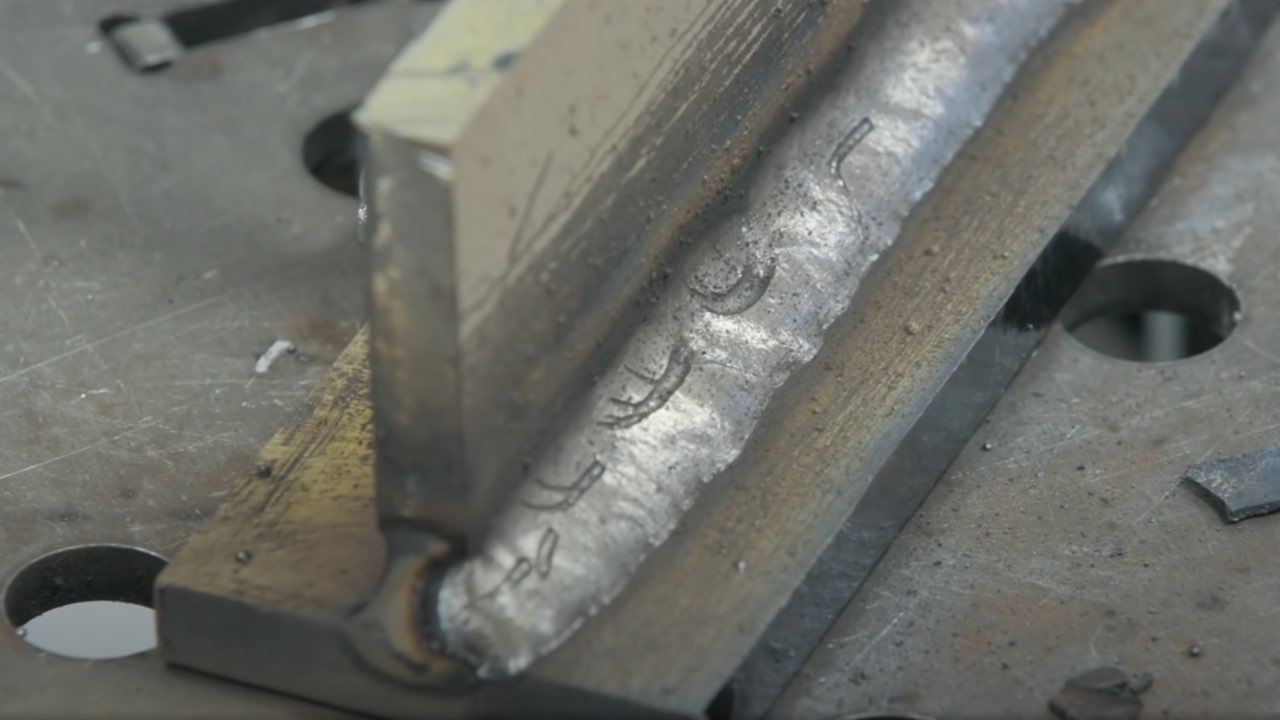
Report this wiki page